Quality Management System
What is the standard about?
ISO 9001 is an international standard dedicated to Quality Management Systems (QMS). ISO 9001:2015 focuses on a continual improvement, process-based approach that supports the effective management of your business. This enables you to meet customers' requirements through an efficient, effective quality management system (QMS). It is suitable for any organisation that wishes to improve customer satisfaction, staff motivation and build a culture of continual improvement. It outlines a framework for improving quality and a vocabulary of understanding for any organization looking to provide products and services
1. ISO 9001
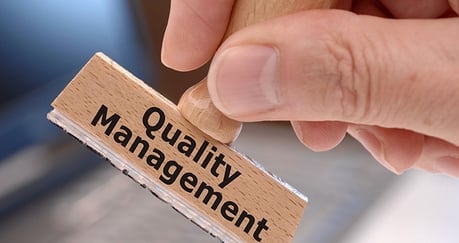
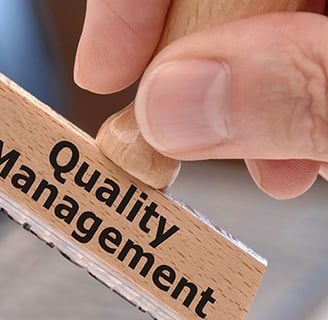
Benefits of implementation
• Strengthening the links between standardization and public policy by providing thought leadership
• Identifying and building national standardization strategies.
• Ensuring the efficient operation by managing financial Sustainability and risk.
• Ensuring participation of, and collaboration with, key stakeholders in all standardization projects.
• Provides continuous assessment and improvement
• Marketing opportunities
• Improved customer retention and acquisition
• Globally recognized standard inviting for international opportunities
2. Total Quality Management- TQM
What is the standard about?
Total quality management (TQM) describes a management approach to long-term success through customer satisfaction. In a TQM effort, all members of an organization participate in improving processes, products, services, and the culture in which they work. Benefits of implementation
• Strengthened competitive position
• Adaptability to changing or emerging market conditions and to environmental and other government regulations
• Higher productivity
• Enhanced market image
• Elimination of defects and waste
• Reduced costs and better cost management
• Higher profitability
• Improved customer focus and satisfaction
• Increased customer loyalty and retention
• Increased job security
• Improved employee morale
• Enhanced shareholder and stakeholder value
• Improved and innovative processes
3. Six Sigma
What is the standard about?
Six Sigma strategies seek to improve manufacturing quality by identifying and removing the causes of defects and minimizing variability i n manufacturing and business process. This is done by using empirical and statistical quality management methods and by hiring people who serve as Six Sigma experts. Each Six Sigma project follows a defined methodology and has specific value targets, such as reducing pollution or increasing customer satisfaction. The term Six Sigma originates from statistical modeling of manufacturing processes. The maturity of a manufacturing process can be described by a sigma rating indicating its yield or the percentage of defect-free products it creates—specifically, to within how many standard deviations of a normal distribution the fraction of defect-free outcomes corresponds.
Benefits of implementation
• Reducing Waste
• Improving Time Management
• Increase Customer Loyalty
• Boost Employee Motivation
• Higher Revenues and Lower Costs
Quality
Solutions
Advisory Services Organization
+91- 022 46026028/ 7710063568/ 8108184275